CONTAINER DRYING DONE RIGHT: HOW CLOROX & JETAIR WORKED TOGETHER TO UPHOLD PACKAGING INTEGRITY
- JetAir Technologies
- Jan 14, 2019
- 2 min read
Updated: Apr 3, 2019
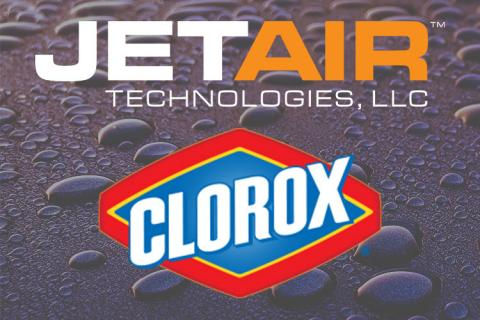
A JetAir container drying system enabled eye-catching, pristine sleeving on Clorox’s 32 oz PET spray bottles.
Almost every American family has The Clorox Company’s products in their home – from the cleaning products and Glad trash bags under their kitchen sinks to the Hidden Valley Ranch and Brita in their fridge. Consumers equate the brand with quality. But every individual working in the consumer packages goods (CPG) market knows that in order to present a quality product, you need quality packaging. To that end, Clorox uses attention-catching shrink sleeving on their 32 oz PET spray bottles. But as in all shrink sleeving applications, insufficient container drying causes consistency problems. Water under the sleeve can lead to bubbles, rippling, or inability to sleeve altogether.
“Like most production facilities, our challenges have been consistency,” explained Eric Smith, Clorox’s Senior Packaging Resource. At one of their facilities, containers were coming out of the filler wet. The system they had installed wasn’t capable of sufficiently drying the containers before they reached the sleever.
Clorox wouldn’t continue with insufficient container drying. “We follow three simple principles here at Clorox: Safety, Quality & Environmental,” Smith said. “They’re all non-negotiable from the top CEO to the newest associate.” Clearly, then, inconsistent packaging couldn’t be sent out from The Clorox Company. It just didn’t fit with their brand.
Rather than run more compressed air and install more air knives onto the line, Clorox contacted JetAir. As container drying experts, JetAir was ready with a turnkey system that could meet Clorox’s dryness specifications.
But did it work?
“The equipment exceeded our expectations. What stands out the most is the ease of installation and how this system integrated within our packaging lines,” Smith said. “I’m in the process of purchasing a third unit for another application.”
With JetAir’s container drying equipment on their line, Clorox was able to maintain production speeds and the quality for which they’re known.
Clorox didn’t just get consistent container drying from their project with JetAir. They also cut costs. “With the new JetAir [system], I don’t have to run plant air to dry the bottles. This savings alone will pay for the JetAir in just a couple of years.”
Container drying is all too often an afterthought. The labels aren’t adhering straightly, or the secondary packaging is falling apart, or the date codes aren’t printing cleanly. It’s then a scramble to purchase air knives and funnel inefficient, expensive compressed air to patch the problem.
Instead of taking that too-frequently trod path, Clorox and JetAir permanently and cost-effectively solved the problem. And, as Smith pointed out, the high ROI means Clorox will see savings on an ongoing basis.
Comments